Bottero innovates with optimized high performance mold-motion
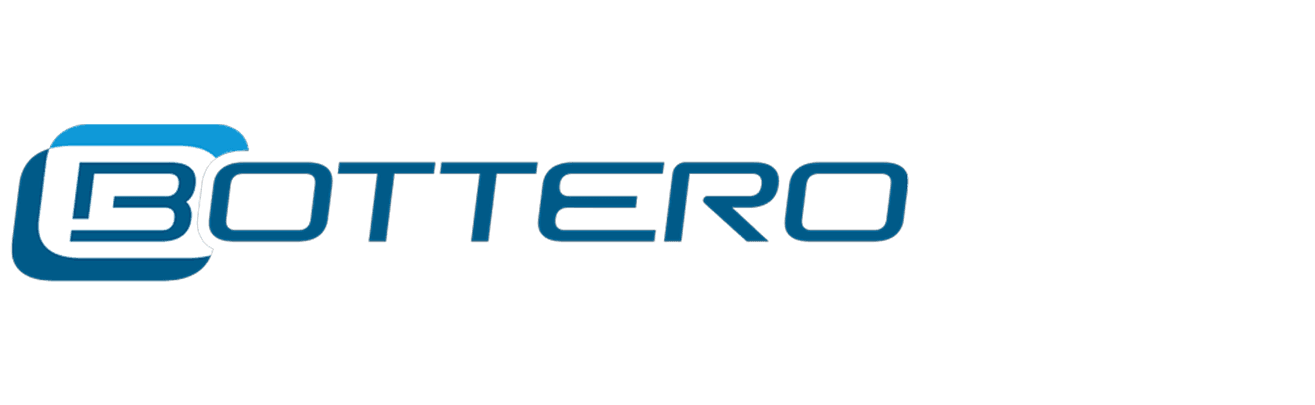
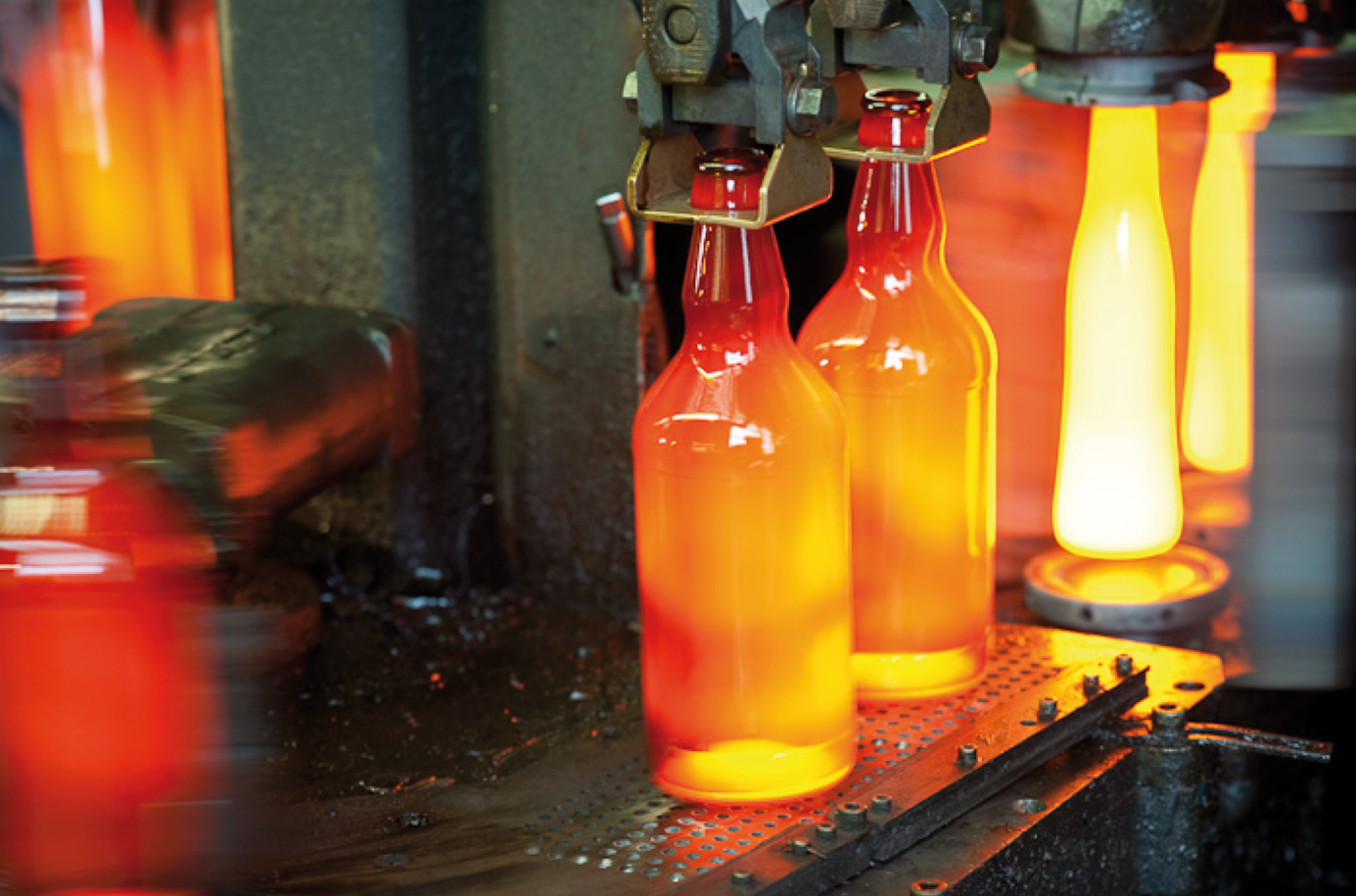
- Company: Bottero
- ESTECO Software Solution: modeFRONTIER
-
Benefits:Find a fine balance between a high number of rigorous constraintsObtain a functioning high-performance designAdjust the model geometry to increase its efficiency and quality
Bottero innovates with optimized high performance mold-motion
Leading in the glass industry is Bottero’s declared ambition. The recent launch of E-MOC, a family of mold opening and closing mechanisms (MOC), has challenged the hollow glass industry. E-MOC introduces a completely new cooling concept, granting the possibility to achieve the proper temperature profile, according to the type of process required for the application field.
“modeFRONTIER optimization approach was the only way to obtain a high-performance design”.
Challenge
“The innovative idea behind E-MOC design is the result of our R&D team’s work: numerous constraints were limiting the possibility of changing the machinery design, so modeFRONTIER, the multi-objective optimization platform, came to our help”, says Marcello Ostorero, Structural and Fluid Dynamics Simulation Department Manager at Bottero. The mechanism had to be equipped with a universal mold holder providing efficient cooling and, when mounted, it had to be readily accessible and installable on both new and existing machines. The optimal system performance called for a smooth and precise mold motion, with fast closing time, and maximum closing and clamping forces.
Solution
The complexity of the problem was tackled with modeFRONTIER within two optimization cycles. The aim of the first one was to minimize mold motion oscillations. The results were then used to conduct a sensitivity analysis, which revealed the piston center movement as the most important variable for mechanism stability, but the geometrical constraints did not allow the piston to maintain the optimal trajectory. This unexpected obstacle was bypassed by replacing the single large piston with three smaller ones. In the second optimization cycle modeFRONTIER guided the model adjustments to minimize mechanism lability and oscillations, while keeping constant the newfound optimal values of component geometries and of piston center movement.
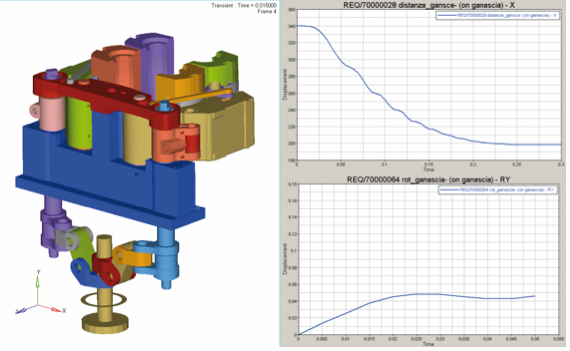
Benefits
“Due to the intricate nature of the required mechanism, the systematic optimization approach proposed by modeFRONTIER was the only way to obtain a functioning high-performance design”, says Ostorero, “modeFRONTIER managed to find a fine balance between a high number of rigorous constraints and adjust the model geometry to the most important mechanism specifications so as to increase its efficiency and quality, while successfully driving a number of software, each solving a single aspect of the problem, integrated in a single workflow”.
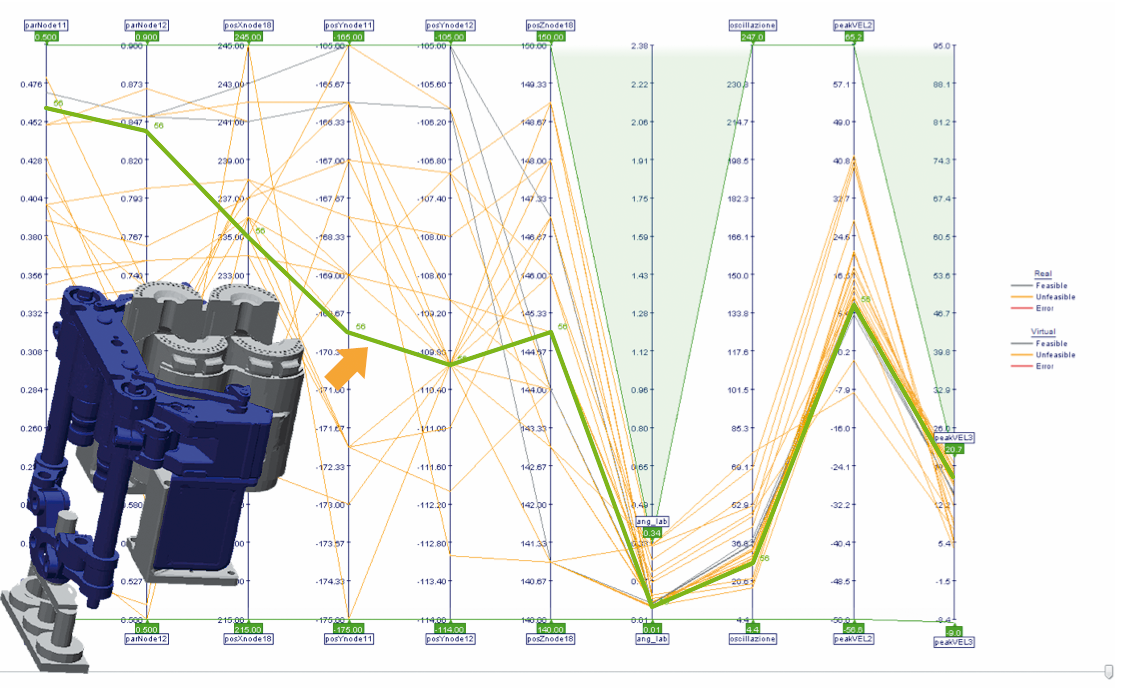
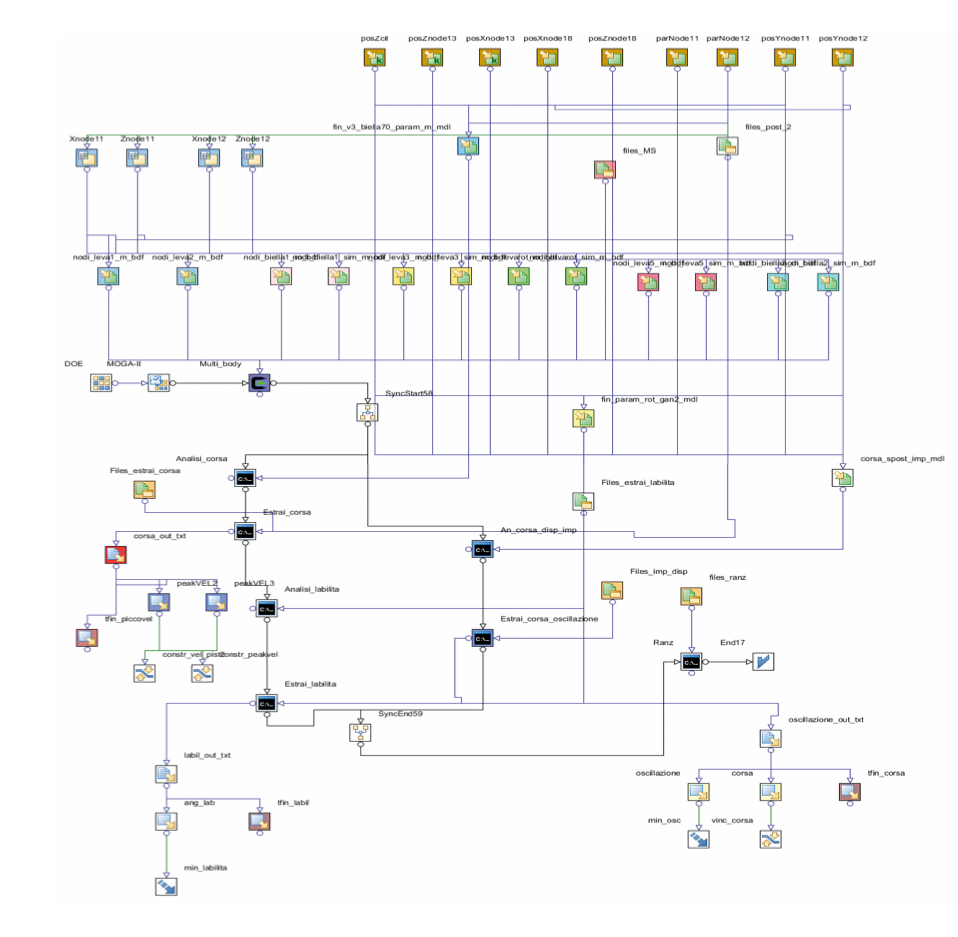
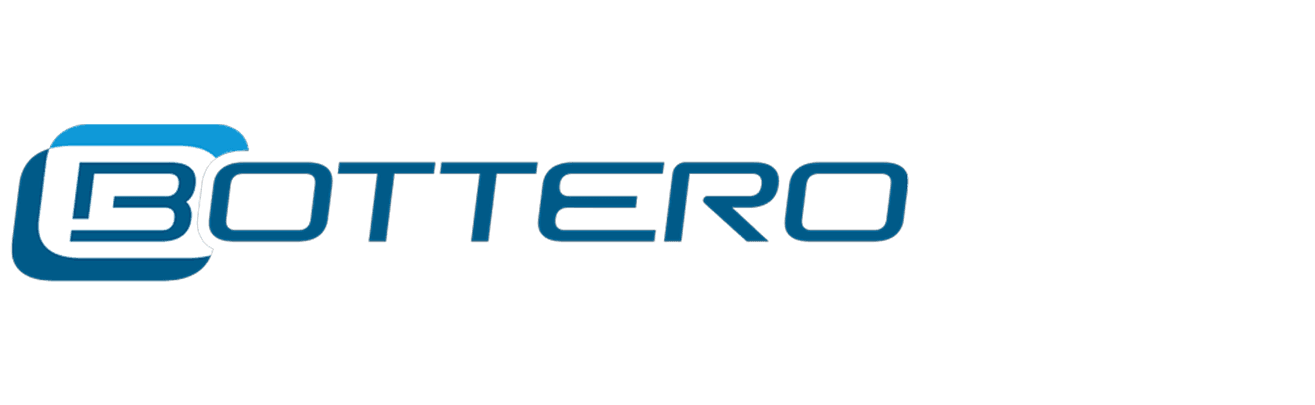
Bottero is one of the world leaders in the glass industry, offering a complete range of solutions in the field of automatic machines for glass processing, in particular glass container production lines, flat monolithic and laminated glass lines and machines, and production lines for float and laminated glass sheets and packaging lines. Headquartered in Cuneo, Italy, the company has been present on the market for over 50 years , with branches and production plants in 7 countries: www.bottero.com