Environmentally friendly aircraft stretches its wings with modeFRONTIER

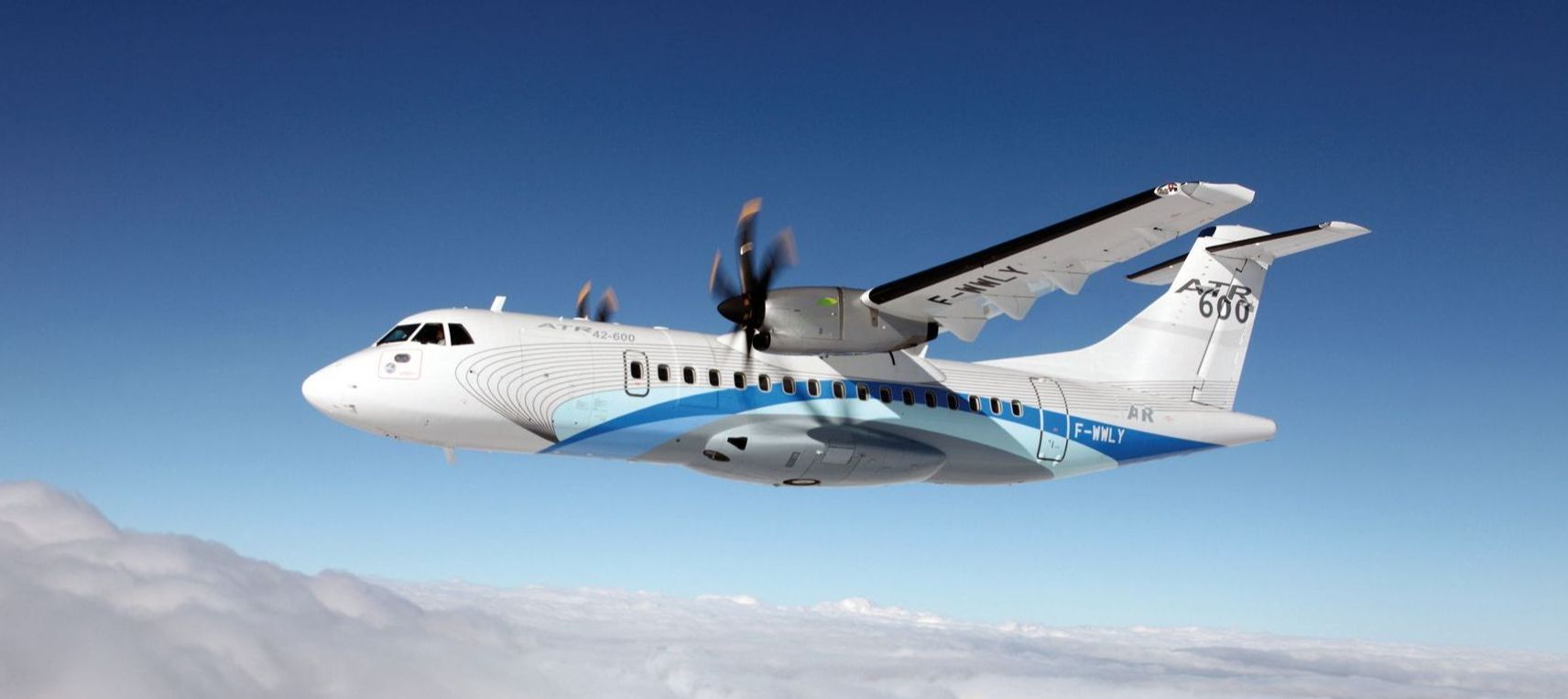
- Company: Leonardo
- ESTECO Software Solution: modeFRONTIER
-
Benefits:Achieve a 2.5% enhancement of aerodynamic performance and a 4% wing weight reductionObtain good aerodynamic results in the 3D analysisGenerate 20,000 design profiles of the 2D wing shape with the design automation process
Aerodynamic performance enhanced by 2.5% and wing weight reduced by 4%
In an ambitious collaborative venture, Leonardo is heading the Green Regional Aircraft (GRA) design team of the The Clean Sky Joint Technology Initiative, committed to developing environmentally-friendly aircraft. The future of domestic air travel lies in: weight reduction, aerodynamic efficiency, high level operational performance, compliance with emission standards and respect of noise limits.
"modeFRONTIER has proven to be an effective tool for the design team, identifying feasible solutions."
Challenge
Targeting multiple objectives such as lowering aircraft drag, wing weight and environmental impact of lower speed conditions (i.e. take-off and landing), enhances overall environmental performance, measured by fuel consumption and noise generation. Seeking the most promising solution for this new generation aircraft, two wing shapes were studied using modeFRONTIER optimization. A “thin” configuration was selected to analyze aerodynamic performance, without any structural restrictions to airfoil thickness; a “thick” configuration was chosen reduce the weight of the wing.
Solution
modeFRONTIER integrated complex objectives, achieving remarkable enhancement for both wing configurations, while still complying with Top Level Aircraft Requirements (TLAR). The design automation process piloted by the modeFRONTIER workflow generated 20,000 design profiles of the 2D wing shape, while incorporating aerodynamic and structural analysis using Leonardo in-house codes. Once the optimal 2D profile was selected, CFD computations were validated by employing a suitable parametric Catia 3D wing-body. Good aerodynamic results were maintained in the 3D analysis.
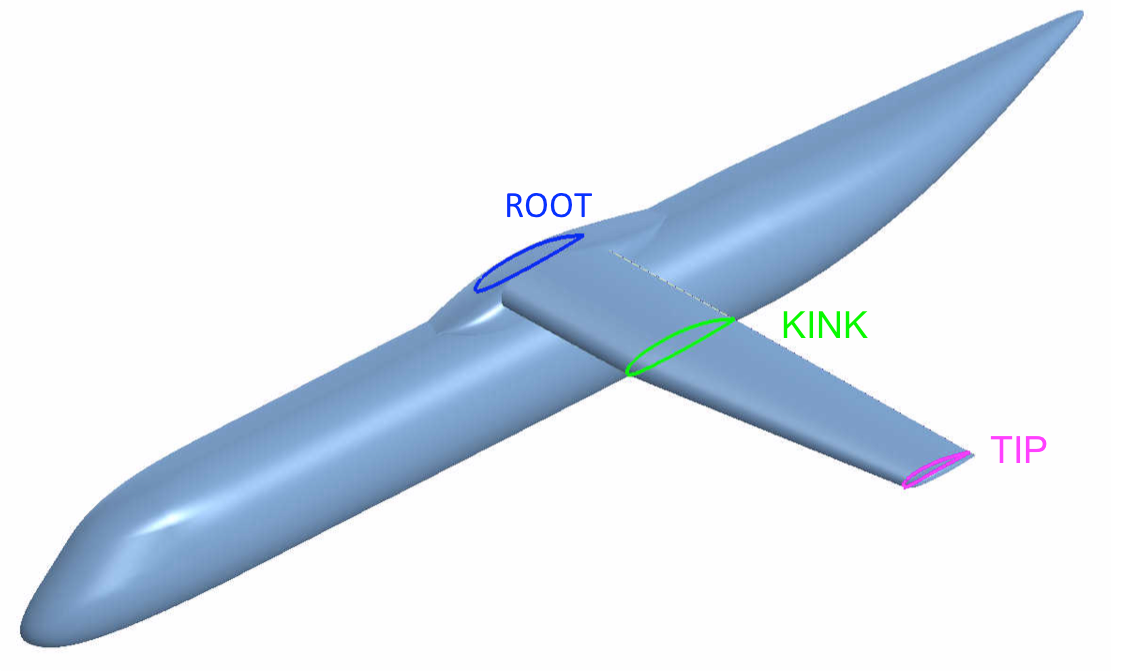
Reference model configuration.
Benefits
“modeFRONTIER has proven to be an effective tool for the design team, identifying feasible solutions and achieving a 2.5% enhancement of aerodynamic performance and a 4% wing weight reduction”, says Enrica Marentino, CFD Specialist at Leonardo. modeFRONTIER successfully streamlined the two-step optimization process for wing shape configuration and its multi-objective genetic algorithm (MOGA-II) was profitably used to solve the optimization problem. Correlations among the aerodynamic parameters were explored thanks to modeFRONTIER statistical tools, providing deep insights which helped set up the optimization strategy effectively. The MCDM tool provided a useful framework towards attaining a ranking for the Pareto front solutions, supporting the design team in determining the best outcome. “The optimized configurations, while still matching TLAR requirements, determined substantial advantages compared to the initial wing profiles”, says Enrica Marentino.
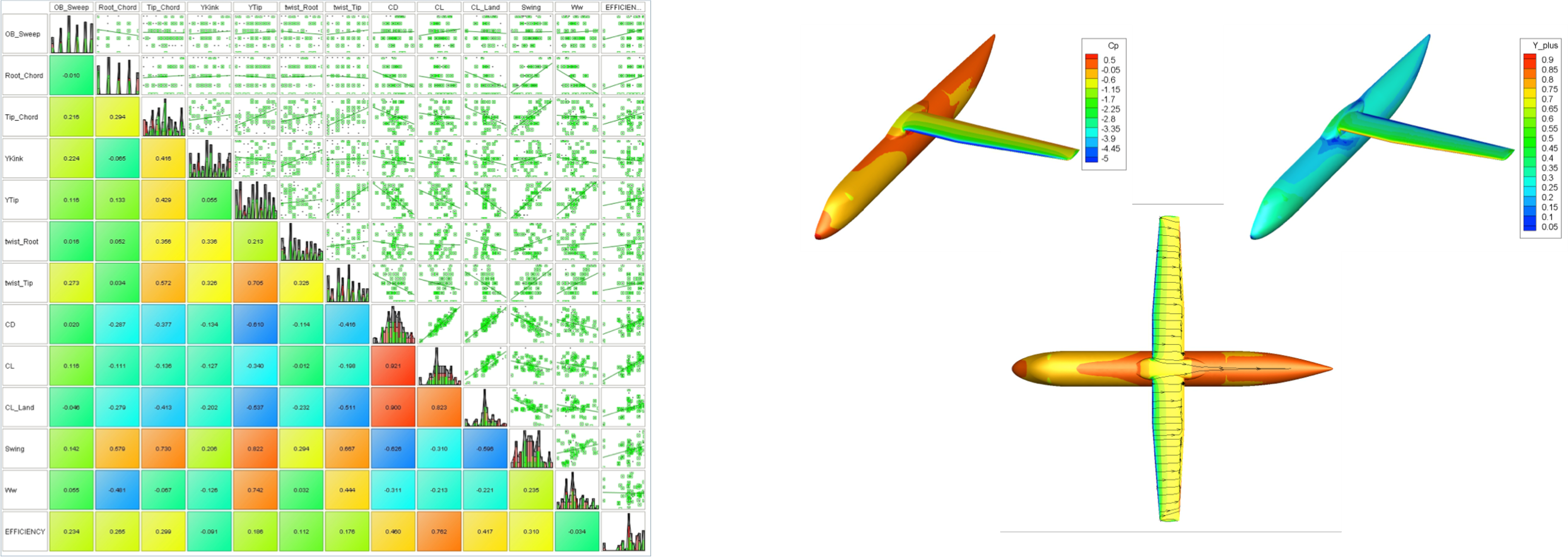

Leonardo is the global player which leads the Finmeccanica aeronautics business by continuously increasing its ability to design, build, integrate and support complex systems for both commercial and defense markets worldwide. In an equal-share joint venture with EADS, it owns ATR, which dominates the regional turboprop market. With the Russian company Sukhoi it is developing and marketing the Superjet 100. leonardocompany.com