ECS System Simulation - Architecture and Performance Optimization from the Early Phases of the System Design

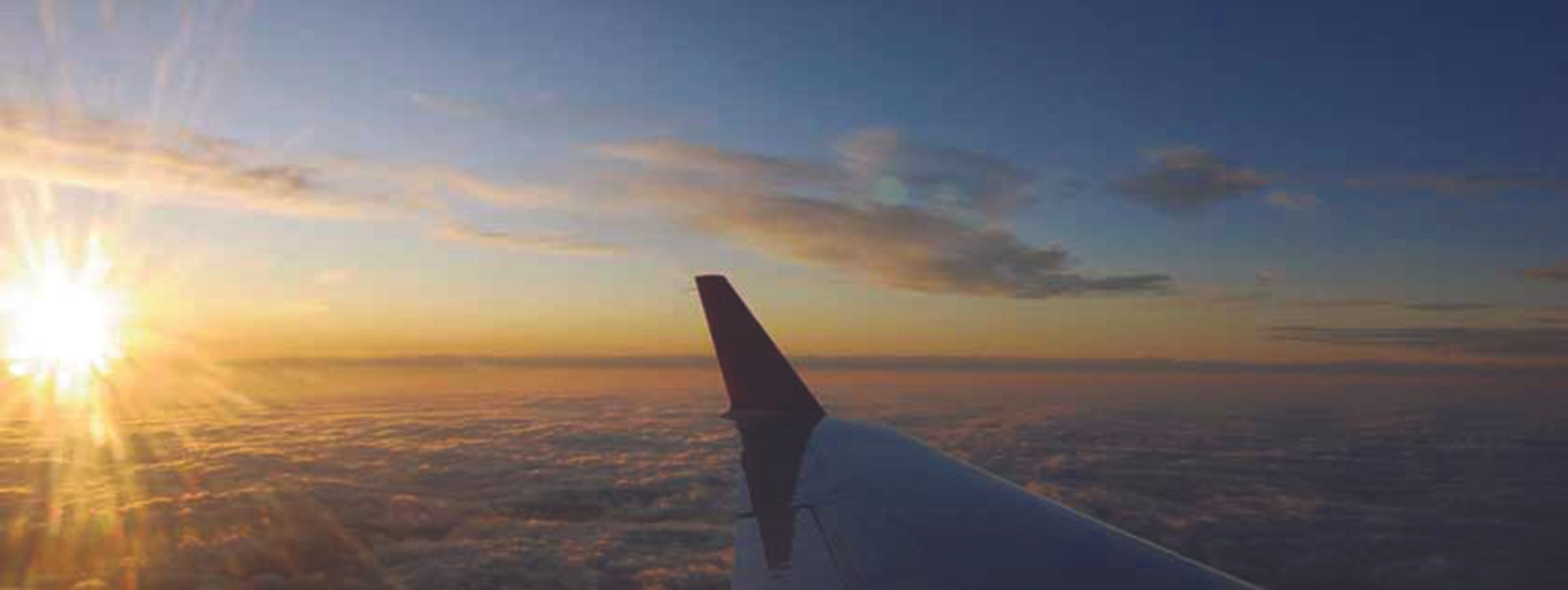
- Company: Leonardo
- ESTECO Software Solution: modeFRONTIER
-
Benefits:Find the best configurations possible for the nozzle shape and refined the thermal architecture designEnhance passenger comfortReduce pressure loss and noise level to the minimum.
ECS system simulation - Architecture and performance optimization from the early phases of the system design
The trend today in aircraft thermal design leans towards electronic system integration requiring higher heat densities and a more frequent use of composite primary structures. All these factors require thermal management and architecture design to achieve a suitable robustness, even in the early design stages. The thermal architecture should be able to prevent the risks of damage to temperature-sensitive equipment and limit the expensive overdesign of aircraft systems.
"The optimization platform helped us reduce pressure loss and noise level to the minimum."
Challenge
The optimization of the thermal architecture is considered one of the key factors of future aircraft development. It requires a composite pyramid of simulation tasks to be set and managed: from equipment to aircraft section simulation to the global aircraft thermal analysis. Adopting this approach gives rise to a number of difficulties due to the variety of physical models to be integrated and the partners, techniques and tools interacting at each level of the pyramid. This case study from Leonardo’s Environmental Control System (ECS) department shows how the different design disciplines involved are handled effectively through process integration and automation, enabling the optimization of the overall performance from the early stages of system design. One of the systems considered in the ECS design at Leonardo is the air conditioning pack and distribution system. The air, supplied from the engine compressor, is processed in the conditioning pack before being distributed to the fuselage compartments. Enhancing the efficiency of the thermal architecture implies several constraints and requirements relating to standards-compliance and safety regulations. Designers must adhere to given A/C configurations and maintain suitable thermoacoustic insulation and temperature levels for both the cabin and cockpit.
Solution
First, engineers at Leonardo used the TPM approach to compare the performance of two alternative architectures, preferring a parallel layout composed of an underfloor and a low pressure air line fed from the mixing chamber and distributing the airflow in parallel through a set of risers. Next, after building the model for the selected architecture and its subsystems in LMS.Amesim, the workflow for the air nozzle shape optimization was built in modeFRONTIER. “The optimization platform helped us reduce pressure loss and noise level to the minimum” says Gaetano Mirra (CTO, General Systems - ECS and Ice protection specialist at Leonardo).
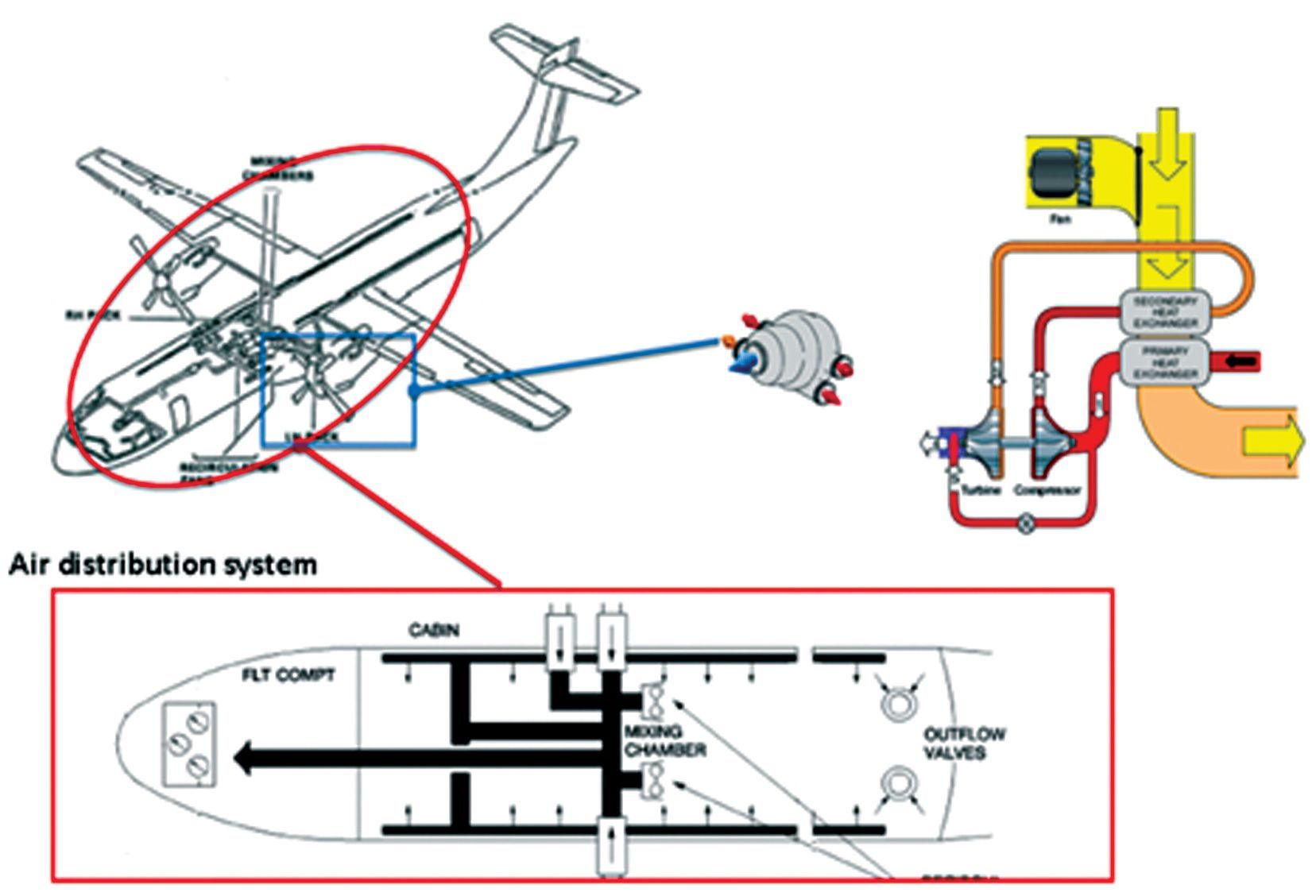
Air flows from the engine processor and through the air conditioning pack before distribution.
Benefits
“modeFRONTIER automation and integration capabilities enabled us to simultaneously consider the fluid dynamic and acoustic analysis and easily handle the data flow including Catia, StarCCM+ ans PostPRO simulations in a unique environment” continued Mirra. “We found the best configurations possible for the nozzle shape and refined the thermal architecture design, further enhancing passenger comfort in terms of cabin thermal environment”.
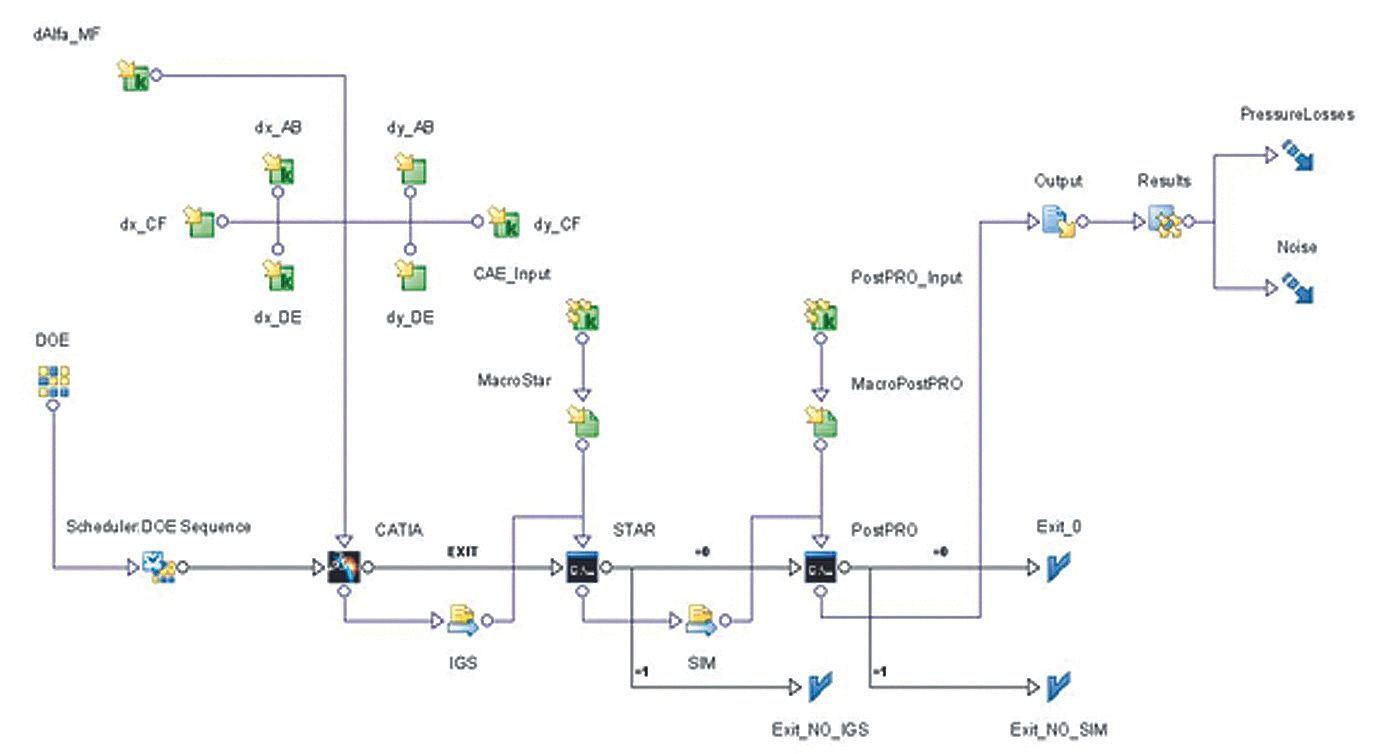
modeFRONTIER workflow for the nozzle shape optimization.
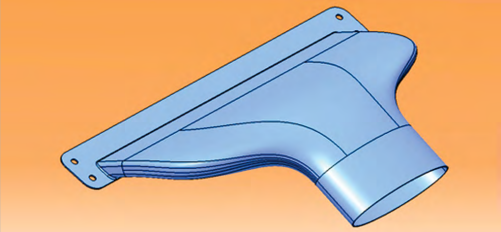
Final product developed after optimization.

Leonardo is the global player which leads the Finmeccanica aeronautics business by continuously increasing its ability to design, build, integrate and support complex systems for both commercial and defense markets worldwide. In an equal-share joint venture with EADS, it owns ATR, which dominates the regional turboprop market. With the Russian company Sukhoi it is developing and marketing the Superjet 100. leonardocompany.com