Diesel fuel efficiency takes shape with optimization

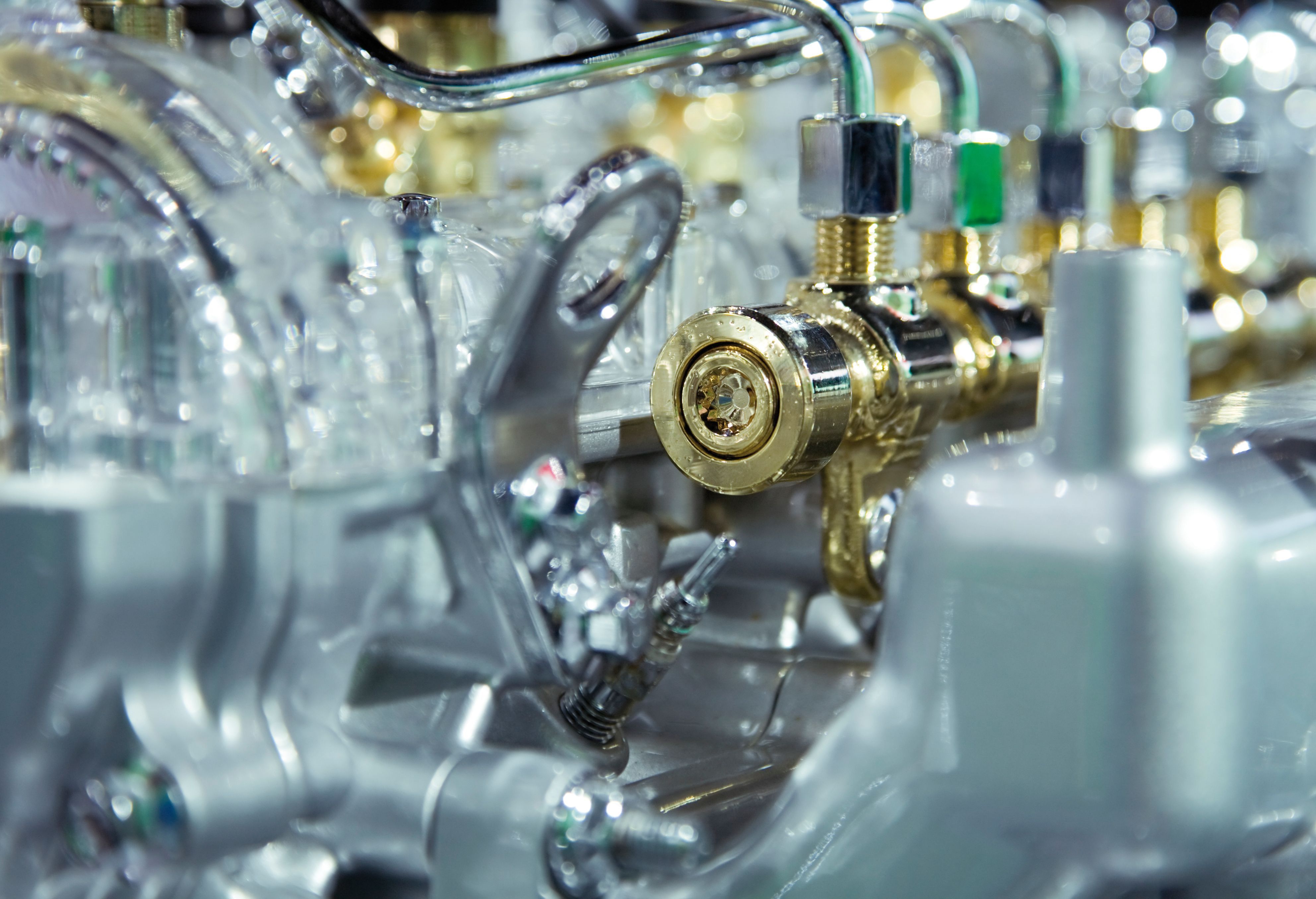
- Company: ISUZU
- ESTECO Software Solution: modeFRONTIER
-
Benefits:Pilot the 3D-CFD simulations with a computational mesh created with CONVERGE CFD and modeFRONTIERImprove fuel consumption by 3.2%Spot the optimal shape
ISUZU Advanced Engineering Center (IAEC) enhances fuel efficiency by optimizing the combustion chamber design
In the debate on how best to tackle the impact of vehicles on environment, the improvement of diesel engine efficiency has emerged as a transitory but effective solution, especially for heavy-duty vehicles and passenger cars. Designers at the ISUZU Advanced Engineering Center (IAEC) have analyzed how to enhance fuel efficiency by modifying the shape of the diesel engine combustion chamber.
"The optimized chamber improved fuel consumption by 3.2% compared to its shallow dishtype counterpart."
Challenge
Theoretical thermal efficiency affects fuel consumption in diesel engines and one way of improving it is to increase the combustion chamber compression ratio. The resulting higher in-cylinder temperature and the expansion of the impingement area between fuel spray and chamber wall, however, can cause the chamber wall to heat up and lower theoretical efficiency. The team at IAEC looked at a new way of lowering heat loss by studying the combustion chamber shape, preventing the volumetric inefficiencies and cost and durability issues, which other methods caused.
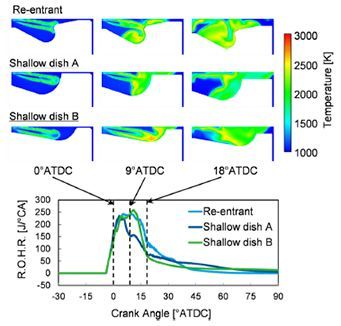
Solution
To analyze the impact of the different chamber shapes, the team first defined the chamber outline and spray angle2 and adjusted it to match a given baseline compression ratio. The computational mesh was then created with CONVERGE CFD and modeFRONTIER was used to pilot the 3D-CFD simulations. “In this way, we were able identify the shapes with the maximum cumulative heat release and work, and – at the same time - the minimum heat loss” says Takashima, Chief Engineer Powertrain Product Planning at IAEC.
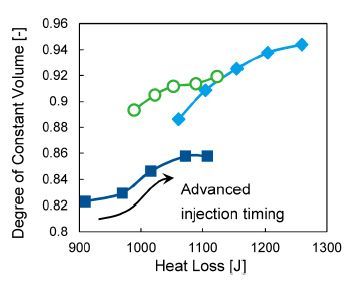
Degree of constant volume vs heat loss.
Benefits
“The shape with the highest cumulative rate of heat release was analyzed in depth. We compared it to calculated heat release rates and cylinder gas temperature profiles of re-entrant-type and shallowdish-type chambers and, later, verified it using experimental data from a single-cylinder engine. The optimized chamber improved fuel consumption by 3.2% compared to its shallow dish type counterpart. modeFRONTIER helped us spot the optimal shape and further analyze the delicate tradeoffs regarding the thermal balance” concluded Arato.
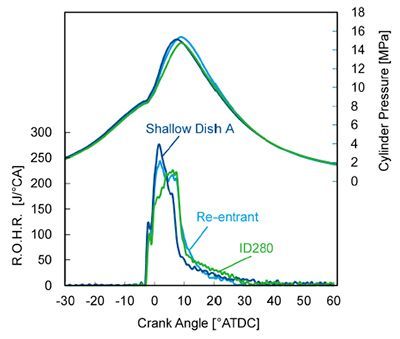

Isuzu Advanced Engineering Center, LTD . (IAEC) was established in 1990 for the purpose of carrying out research on future technology necessary for the product development of Isuzu vehicles. The team performs research related to commercial vehicles and diesel engines in 3 main fields — vehicle safety, environmental conservation, and energy conservation. IAEC is committed to achieving the ideal automobile for an ideal future by forming organic relationships with engineers and researchers from R&D and educational institutions around the globe. www.iaec.isuzu.co.jp/en/