American Magic perfects AC75 design for the 36th America's Cup
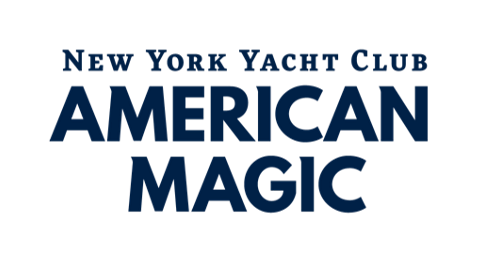
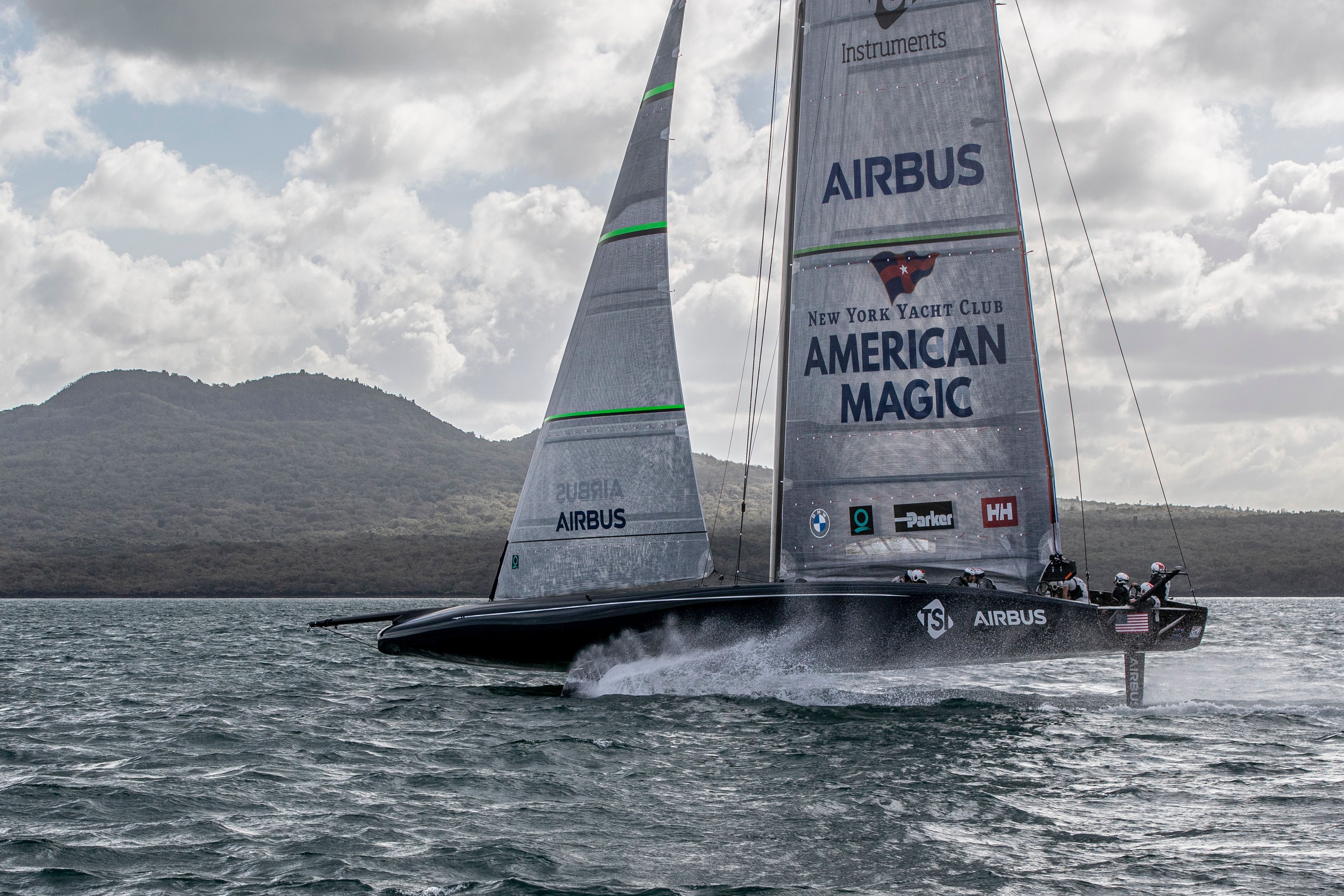
- Company: American Magic
- ESTECO Software Solution: modeFRONTIER
-
Benefits:Manage design and optimization from the exploratory phase to post-processing and decision makingTailor the strategy in a flexible way: from Design of Experiment (DOE) to Sensitivity Analysis and multi-strategy algorithmsProcess automation, intelligent algorithms and advanced post-processing capabilities enable engineers to deliver optimized solutions faster
The America’s Cup isn’t just the first sailing competition in history, it’s also the first when it comes to innovation. Learn how American Magic engineers partnered with ESTECO to prepare for their next challenge. Using modeFRONTIER in different phases of the design process, they integrated geometry changes, performed hydrodynamic CFD simulations and explored different optimization strategies.
"Using modeFRONTIER process automation, intelligent algorithms and decision making capabilities enables us to decrease foil optimization time from 3 weeks to 4 days."
New design challenges: monohulls that fly
The America’s Cup is the oldest and most important trophy in sailing. What makes it unique is that the reigning champion gets to decide the rules for the next edition, like the date and the location. More importantly, it defines boat class and design rules.
The 33rd America’s cup in 2010 pushed the boundaries of boat design by introducing new technologies, design concepts and materials. When BMW Oracle pitted its 34-meter trimaran and 55-meter high rigid wing against Alinghi in the first regatta, it won by 15 minutes, sailing at more than 18 knots in 8 knots of wind. The 36th America’s Cup builds on changes to previous edition class rules with a new boat concept: a monohull racing boat that doesn’t sacrifice the concept of flying boats. Two t-shaped side foils guarantee that the boat flies above the water. Engineers can’t rely on previous experience and now find themselves having to design a completely new boat. Moreover, competition rules allow teams to design only certain parts of the boat, like foil wings, sails, hulls and systems, while others must be designed by third parties. Whereas the foil wing structure and profile can be designed by teams, the arm structure is determined, designed, and built by a supplier company.
American Magic is using ESTECO technology in each phase of the design process, from concept to the refinement of foils and sails. Specifically it uses modeFRONTIER. Its process automation, intelligent algorithms and advanced post-processing capabilities enable engineers to deliver optimized solutions faster.
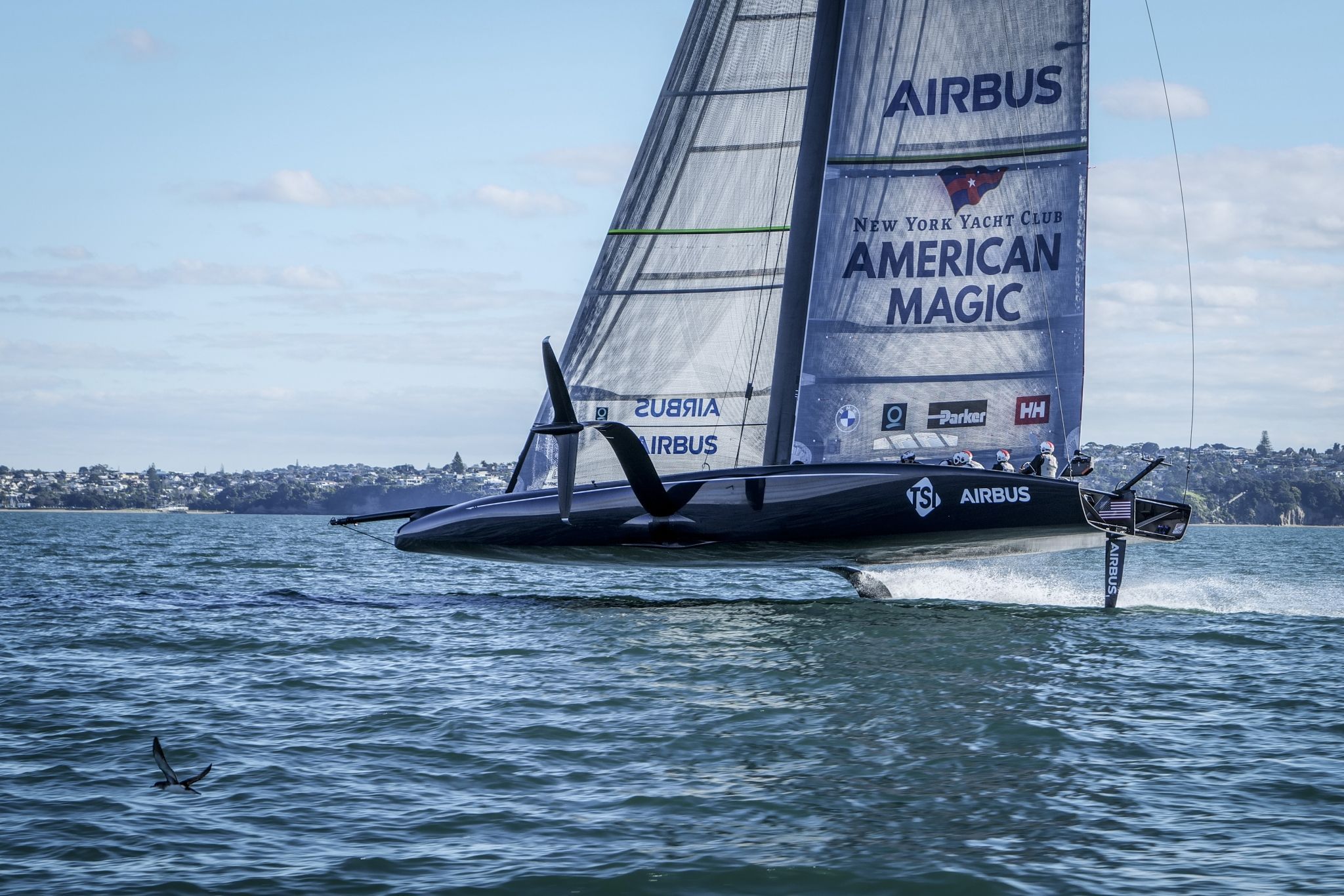
Complex simulation studies on foil and mainsail geometries
The AC75 has two t-shaped side foils. The arm is attached to the hull with a moving joint which allows the crew to move the foils in and out of the water according to the sailing mode. On the other end of the arm is the foil itself. The foil has a main airfoil profile section coupled with moving flaps. Internally, enough space must be guaranteed for the systems to operate the flaps. Foil design is challenging because it involves the simulation of myriad geometries in different configurations and under multiple operating conditions - all of which determine boat performance. Foils need to create low drag but generate enough force to enable the boat to lift at the start and fly during the race. Righting moment is required to balance the heeling moment of the sails. At higher speeds, cavitation can cause significant loss in performance. Stability is fundamental, especially during maneuvers.
In the first stage, hydrodynamic performance is computed using a low-fidelity solver that takes into account the different operating conditions - namely speed, sailing mode and position in the water. In the second stage, the full 3D geometry is designed and evaluated using CFD simulations. High-fidelity simulations can’t be used directly in the first stage of development due to lengthy computational times. The sail plan is composed of the mainsail and a jib or code zero, which are interchangeable. All dimensions are restricted by rules, so engineers can optimize the shape within specific limits. The mainsail is a twin skin sail that acts like an airfoil. By adjusting mast rotation, twist and boom position, the 3D geometry of the mainsail can be tuned for different wind speeds and sailing modes foils, the aerodynamic forces are tuned to generate lift, maintaining momentum and low drag.
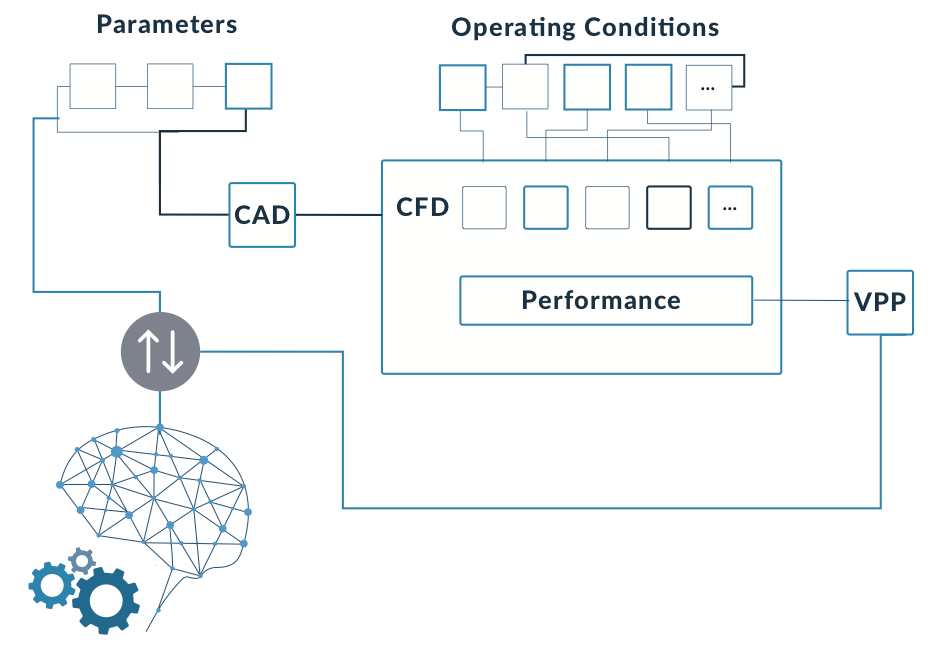
Getting foil and sail design just right
American Magic engineers are using several simulation software for the foil and sail design which consists of three steps: geometry definition, force computation and boat speed estimation. The entire process is automated in modeFRONTIER. Multiple workflows handle input modifications, the execution of different tools and file and data exchange.
Mares, developed by Airbus, handles the geometry generation of the airfoil and the flap, considering different combinations. Hydrodynamic forces generated by the foil, lift, drag and momentum, as well as cavitation speed are obtained through CFD simulations. The designers use a low fidelity 1D potential-based code in the initial phases to evaluate multiple configurations in a small amount of time. American Magic uses a RANS-based tool to perform high fidelity 3D simulations in the final refinement and optimization phase. Both Mares and the CFD tools are coupled with modeFRONTIER using Easydriver nodes. This enables them to couple their in-house tools using input and output files and customize execution scripts. Geometry consistency is guaranteed by constraints that filter out weird shapes and meet requirements for internal cabling and mechanisms as well as cavitation limits.
The main goal of the optimization is to minimize drag for specific lift values. It isn’t enough to understand the efficacy of a foil shape. It’s important to understand how the boat behaves. An in-house Velocity Prediction Program (VPP) software estimates the overall boat performance at different wind speeds and sailing modes. The software uses forces generated by foils and sails to find the overall boat equilibrium and predict boat velocity. A nested modeFRONTIER workflow handles different operating conditions. These are sequentially run, using internal loops to compute the global performance of the design. Multiple operations are handled in parallel to make the most of computational resources. Once the forces are solved, these are passed on to the VPP calculation. Foil and sail design share most of the process and simulation tools but defining the geometry is more complex. The mainsail is divided into several sections where each section can have a different shape based on input values. On top of this, optimal adjustments for every shape need to be calculated. This results in large numbers of configurations which are run to find the best design. It’s fundamental to formulate constraints based on maneuverability, considering adjustments that are feasible for the crew - optimal solutions have no meaning if they are too complex to be performed during the race.
Each design phase requires a different optimization strategy. In early stages, genetic algorithms guarantee robustness to find the global optimum in a large design domain. In the last phase, it’s important to cut optimization time - conventional techniques aren’t feasible. Therefore, multi-strategy algorithms are used in combination with advanced initialization techniques to speed up the whole optimization process.
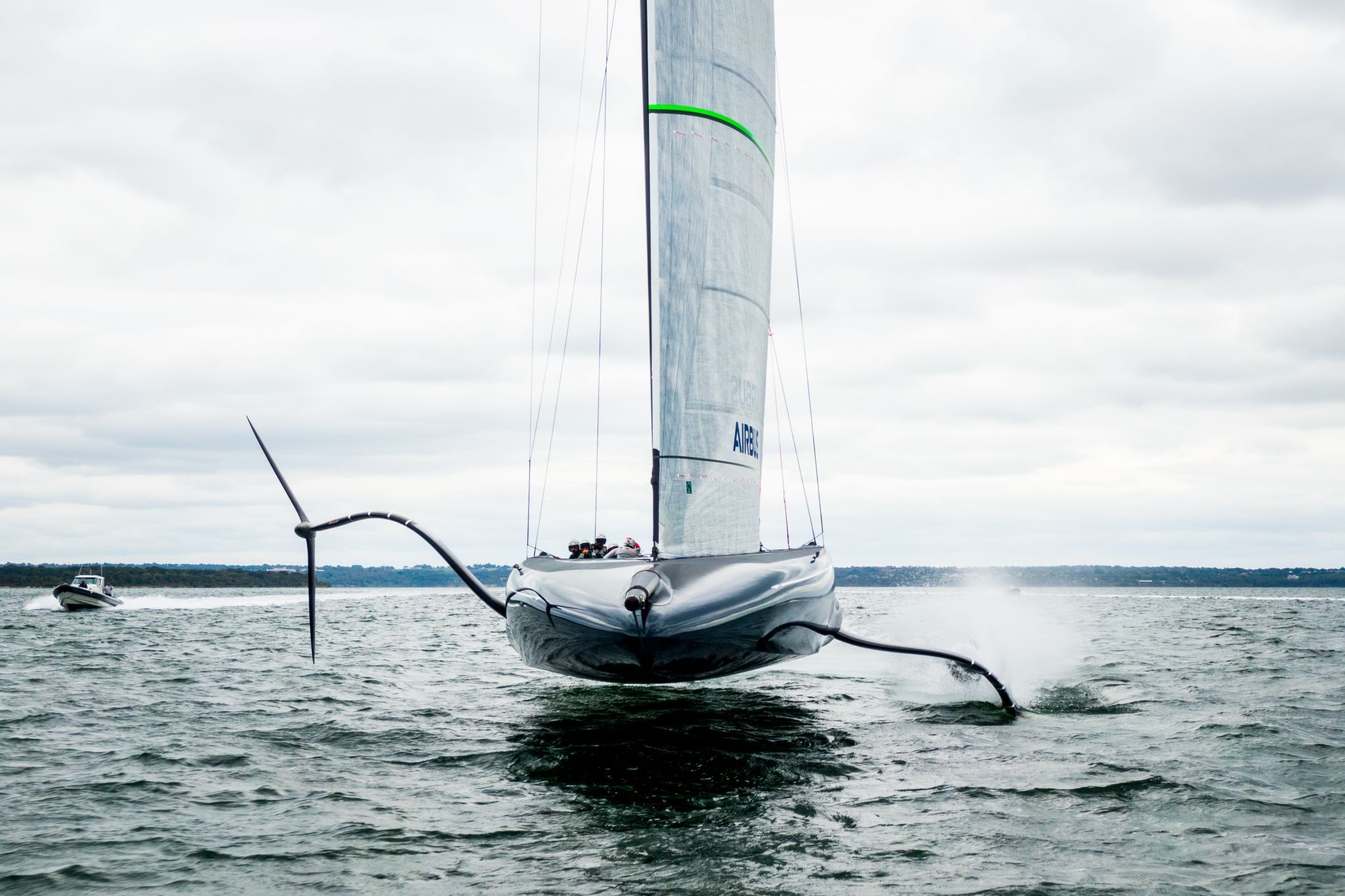
"Working side-by-side with ESTECO engineers enables us to pool our respective expertise to get the most out of modeFRONTIER."
American Magic and ESTECO - partners in innovation
The American Magic design team relied on ESTECO technology in the design and optimization of the boat. Paolo Motta, Performance Prediction Engineer says, “The AC75 is a complex racing boat with interacting subsystems. This makes the design process a challenging and time-consuming task. Using modeFRONTIER process automation, intelligent algorithms and decision making capabilities enables us to decrease foil optimization time from 3 weeks to 4 days. This gives us time to discuss and think about present challenges and develop new solutions”. According to Arthur Rozand, Performance Prediction Engineer, “The key benefit of using modeFRONTIER is to have a suite of tools in one place. In this way it’s easy to manage design and optimization from the exploratory phase to post-processing and decision making. Time is a constraint in development. With modeFRONTIER, we have the flexibility to tailor the strategy. For example, in the early stages of development, DOE strategies and the sensitivity analysis tool help us understand which design variables are the most important. In the final stage of development we use multi-strategy algorithms and advanced charts to select the best design.” “Our partnership with ESTECO is bringing in great results.” says Giorgio Provinciali, Velocity Prediction Program (VPP) Lead, “Working side-by-side with ESTECO engineers enables us to pool our respective expertise to get the most out of modeFRONTIER”.
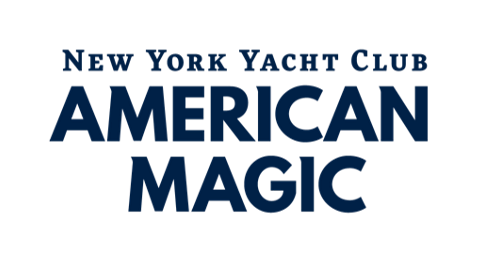
Formed in October 2017 by Bella Mente Racing, Quantum Racing and the New York Yacht Club, American Magic represents a joint vision to win the America’s Cup, the highest prize in sailing and the oldest trophy in international sports. American Magic brings together two highly successful racing programs with one of the foremost yacht clubs in the world, united by a campaign to win back the Cup, reconnect the American sailing base with the premier event in the sport and elevate the quality of competitive sailing in the United States. The name, American Magic, is a nod to the New York Yacht Club’s storied America’s Cup history; a combination of the boat the trophy is named for, and the first boat to defend it.americanmagic.americascup.com